아이스크림 좋아하시나요? 컵에 담겨 떠먹는 아이스크림도, 콘 위에 얹어 먹는 아이스크림도 좋지만, 제가 개인적으로 가장 좋아하는 아이스크림은 바(bar) 형태, 일명 ‘하드’입니다. 가느다란 나무 막대기를 손 끝에 잡고 아이스크림을 한입, 두입 먹다 보면 어느새 막대기만 남게 되죠. 혹여 아이스크림이 녹아서 바닥에 떨어질까, 나무 막대기 아래로 흘러내릴까 단숨에 먹게 되는, ‘재밌는’ 맛이 있습니다.
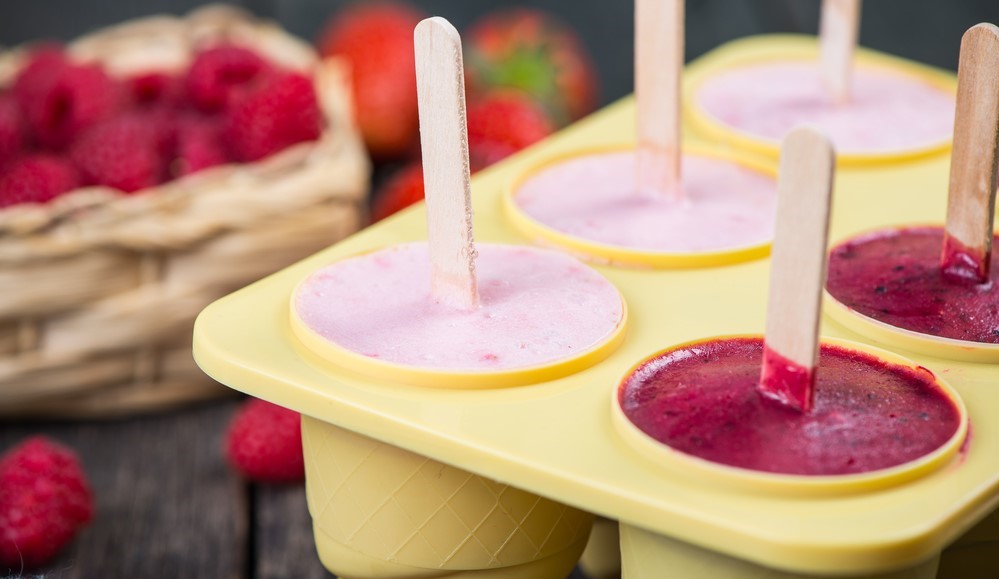
‘하드’는 어떻게 만들까요? 먼저 아이스크림을 담는 틀에 손잡이로 사용할 ‘나무 막대기’를 넣습니다. ‘틀’ 안에 나무 막대를 넣은 상태에서 아이스크림 ‘재료’를 붓습니다. 이 상태로 냉장고에 넣고 얼리면, 막대 손잡이가 꽂힌 아이스크림이 완성됩니다. 막대기는 자연스럽게 아이스크림에 붙어 있게 됩니다.
참 쉽죠? 이와 같은 아이스크림 제조법을 이해하셨다면 인서트 사출도 문제 없습니다. 오늘 ‘제조 길잡이’에서는 ‘인서트(insert) 사출’에 대해 알아보겠습니다.
금속과 플라스틱 결합, 안경테부터 항공부품에도 적용
인서트 사출의 ‘인서트(Insert)’는 ‘삽입하다’란 뜻입니다. 틀 안에 재료를 부어 찍어내는 사출성형 과정에 금속 부품과 같은 별도의 재료를 삽입하여 함께 완성품을 만드는 것입니다. 틀 안에 삽입물을 미리 넣고 적절한 위치에 배치시킨 뒤 틀 안에 재료를 붓습니다. 보통 삽입물은 금속 부품이, 재료로는 열가소성 플라스틱이 많이 사용됩니다. 결과물은 금속 부품과 플라스틱 완성물이 결합된 형태로 나옵니다. 금속과 플라스틱의 접합력이 높아 단단하게 고정되지요.
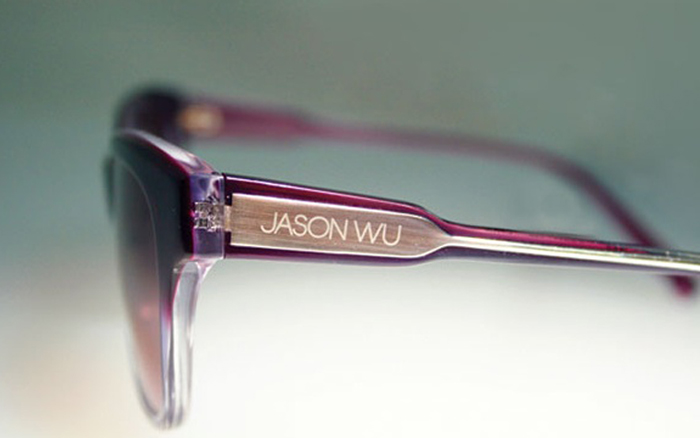
두 가지 재료를 이용해 <위 사진>과 같은 안경테를 만드는 과정을 가정해 보겠습니다. 안경테 일부는 플라스틱으로, 일부는 금속으로 만든다면, 먼저 각각의 재료로 부품을 만든 뒤 이 둘을 붙이는 방식을 떠올리기 쉽습니다. 하지만 인서트 사출을 이용하면 ‘붙이는’ 단계가 필요 없습니다. 플라스틱 안경테를 만들기 전에, 먼저 만든 금속 안경테 부분을 넣어두고 나머지 부분에 플라스틱을 부어버리면 되니까요.
인서트 사출로 만들 수 있는 제품은 규모를 가리지 않고 다양합니다. 국방, 항공우주 분야에 사용되는 거대한 부품부터 의료, 전자, 산업, 소비자 시장까지 다양한 분야를 넘나들죠. 인서트 사출로 만든 제품은 주로 금속과 플라스틱이 결합된 제품이 많습니다. 가위나 스크류 드라이버, 전자제품 코드 선, 나사선이 결합된 플라스틱 물건 등 우리 주변 곳곳에서 인서트 사출로 만들어진 제품들을 찾아볼 수 있습니다.
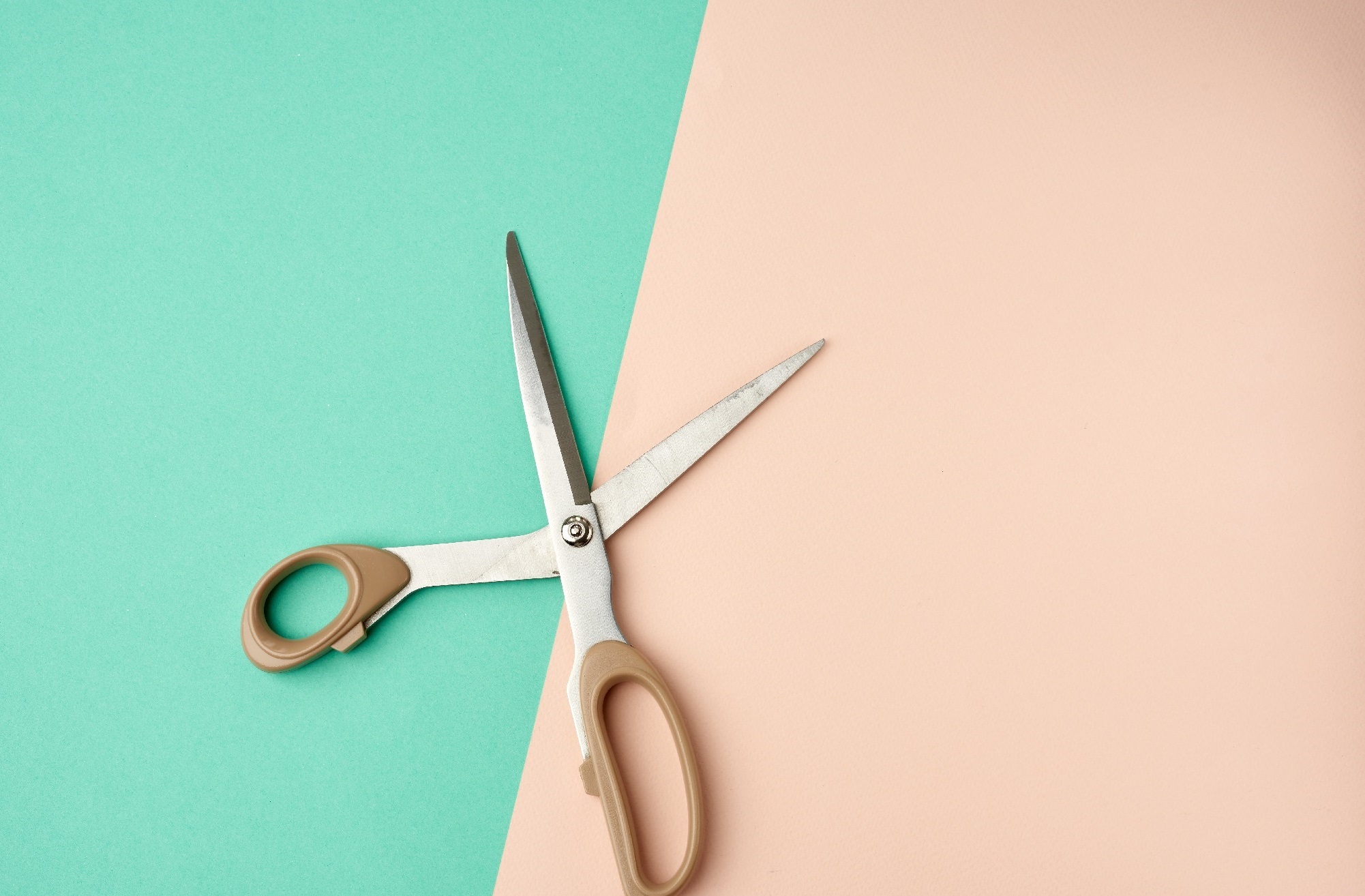
‘녹이고, 집어넣고, 붓는다’··· 인서트사출 3단계
인서트 사출은 일반적인 사출과 마찬가지로 열가소성 재료, 주로 열가소성 플라스틱을 사용합니다. 열가소성이란 열을 가하면 가하면 액체처럼 녹고, 시간이 지나면 형태가 변한 상태로 굳어버리는 성질을 말합니다. 열가소성 플라스틱은 가열하면 녹아 액체 상태가 되기 때문에 금형 모양대로 제품을 만들어내는 사출성형 재료로 적합합니다.
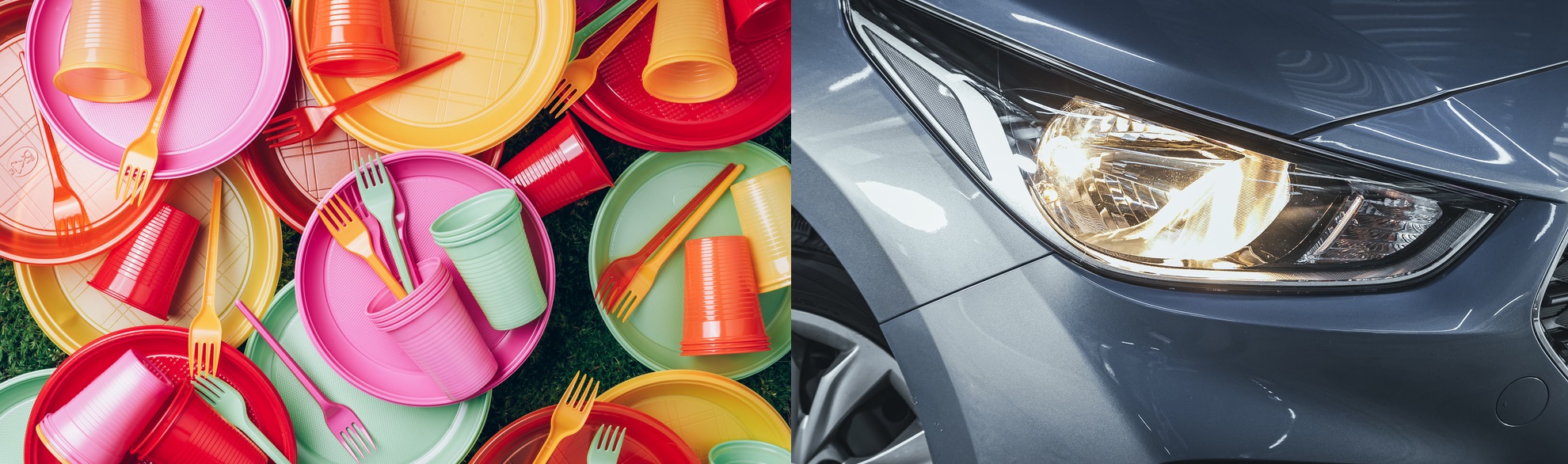
인서트 사출은 크게 3가지 단계를 거치게 됩니다.
첫 번째 단계는 재료를 녹이는 단계입니다. 제품의 주재료인 열가소성 플라스틱을 틀에 주입하려면 먼저 액체 상태로 만들어야 합니다. 특히 액체 상태의 플라스틱이 중간에 굳지 않고 금형에 잘 흘러들어갈 수 있도록 사출기 내 바렐(재료를 틀로 주입하는 관) 주변에도 전기히터가 작동됩니다.
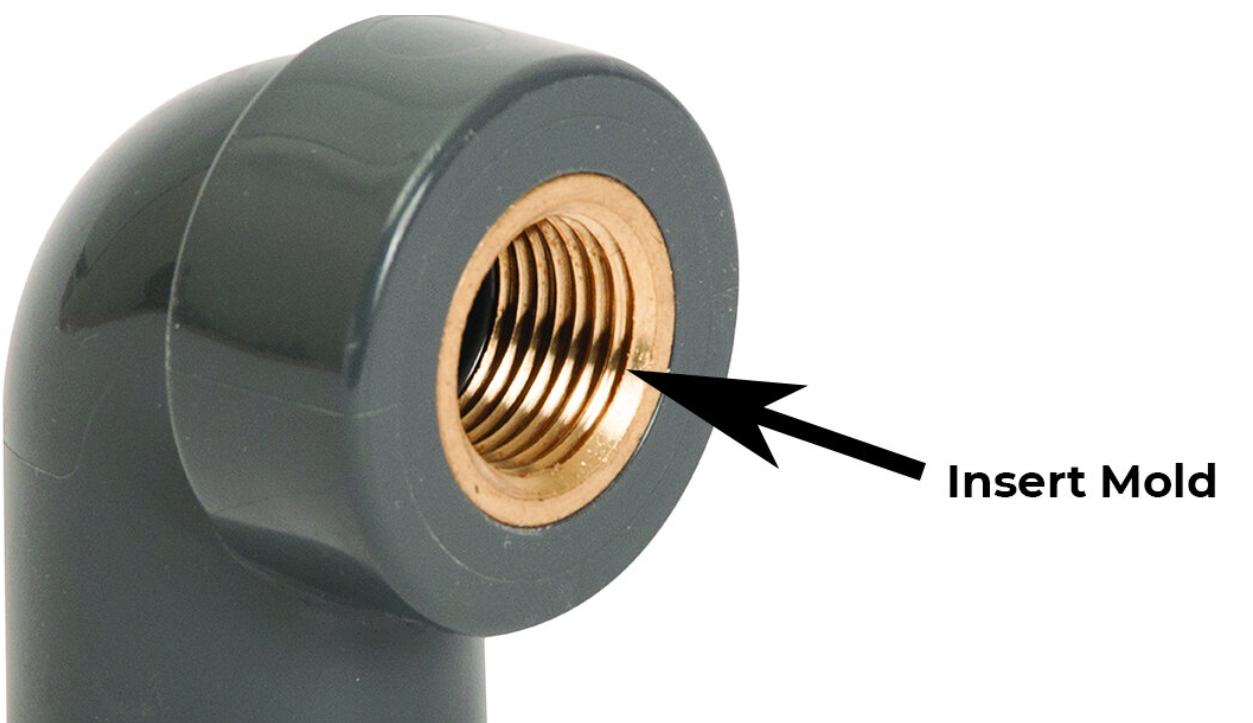
두 번째는 ‘삽입(인서트)’하는 단계입니다. 사출품과 결합할, 다른 재료로 만든 부품을 삽입하는 단계입니다. 삽입하는 부품은 대부분 금속 부품입니다. 금형 틀 안에 플라스틱 수지를 주입하기 전에 미리 부품을 삽입해둡니다. 부품은 공장 내 로봇 팔이 움직여 자동으로 옮기기도 하고 사람이 직접 수동으로 옮기기도 합니다.
마지막 세 번째 단계에서는 금형 틀을 닫고 재료를 주입합니다. 미리 삽입된 금속 부품은 플라스틱 수지가 굳으면서 자연스럽게 접합됩니다. 따로 접합 혹은 조립하는 단계를 둘 필요 없이 제품이 완성됩니다.
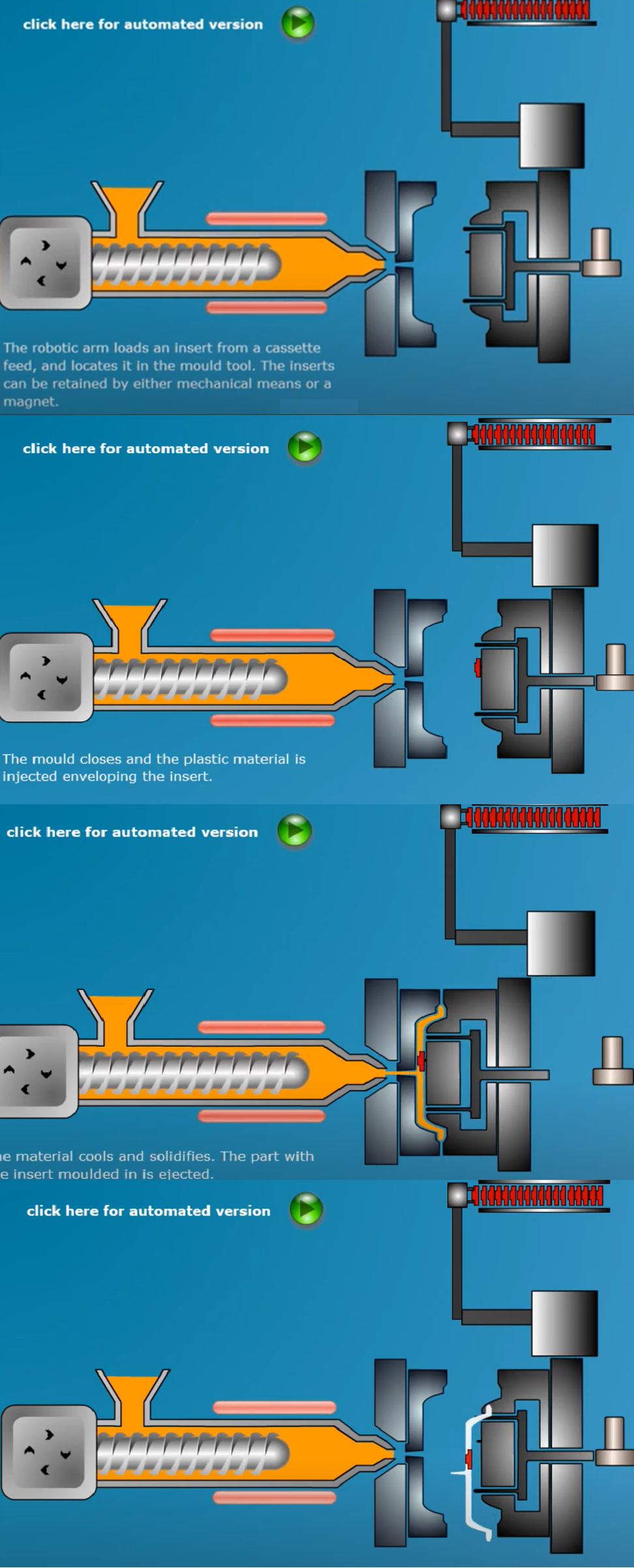
앞서 설명한 대로 인서트 사출에서는 조립 단계가 생략됩니다. 제품 생산시 조립 공정에 적지 않은 시간이 소요돼 소위 ‘병목 현상’이 발생하곤 한다는 점을 감안하면 인서트 사출로 대량생산을 하면 제품 제조 과정에서 한 단계가 줄어들어 시간과 비용이 크게 절감됩니다.
금속과 플라스틱의 장점 동시에 채택
또한 일반적으로 플라스틱 제품은 금속 제품보다 내구성이 떨어집니다. 하지만 디자인을 유연하게 만들 수 있고 무게가 가볍고 비용도 적다는 점 등 플라스틱을 쓸 수 밖에 없는 이유들이 많습니다.
금속과 플라스틱이 결합한 인서트 사출을 이용하면 두 재료의 장점을 모두 활용할 수 있습니다. 제품 중 특히 강도가 높아야 하는 부분은 금속 인서트를 사용하고, 나머지 부분은 플라스틱으로 만든다면 100% 금속 제품보다 무게를 줄이면서 100% 플라스틱 제품보다는 더욱 단단해집니다.
<아래 사진>의 드라이버처럼 제품 특성상 특정 부분만 마모나 열에 잘 견디면 되는 경우라면 해당 부분만 금속으로 만들어도 될 것입니다. 전체 제품을 금속으로 만들지 않아도 되기 때문에 비용을 아낄 수 있고, 필요한 부분의 수명은 연장되기 때문에 제품의 안정성은 높아지게 됩니다. 인서트 사출을 적용하기에 적합한 사례입니다.
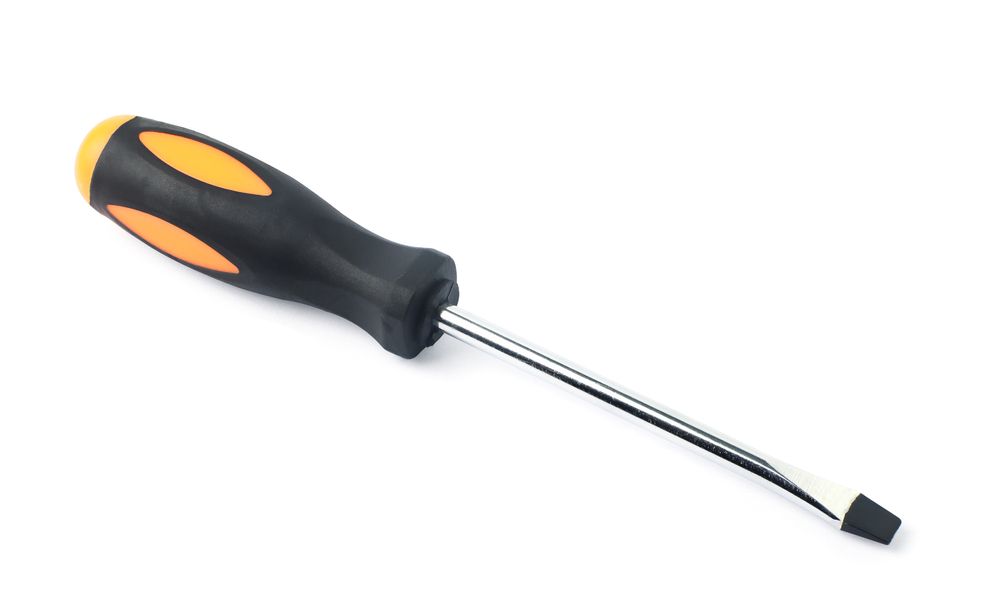
상이한 재료 사용, 복잡한 설계는 비용상승 요인
인서트 사출이 비록 접합(조립)하는 공정을 단축한다고 하지만, 서로 다른 재료를 이용해 두 가지 부품을 따로 만들어야 하기 때문에 단일한 형태로 사출하는 경우에 비해 비용이 비쌀 수밖에 없습니다. 특히 삽입물로 사용되는 금속 부품은 CNC 가공과 같은 금속 성형 공정을 거쳐야 하는데, 이 또한 가공비용이 만만치 않습니다.
또 인서트 사출은 보통 금속과 플라스틱을 모두 다루기 때문에 제품을 설계할 때 두 가지 기술의 설계 방식을 이해해야 합니다. 사전에 두 가지 기술의 특성을 숙지한 상태에서 설계가 이뤄져야 하고, 실제 가공 단계에서도 이들의 특성을 고려해 제조가 이뤄져야 합니다. 비용 측면에서는 마이너스 요인이라 할 수 있습니다.
온라인 제조 플랫폼 캐파(CAPA)에서는 ‘인서트 사출’과 CNC를 비롯한 2300여(공정 합산 기준) 제조업체들이 파트너로 참여하고 있습니다. 아래 캐파 홈페이지에 접속해 도면과 함께 요청사항을 적어 주문을 의뢰(3분이면 작성 완료!)하면 24시간 내에 평균 7곳의 파트너 업체로부터 무료로 견적을 받아볼 수 있습니다.