“I’ll be back!” 터미네이터가 용광로 속으로 들어가며 우리에게 남긴 한 마디입니다. 터미네이터가 용광로 속으로 서서히 사라지는 모습을 다시금 떠올리면서, 저는 터미네이터의 엄지 손가락보다도 펄펄 끓는 용광로에 눈길이 갔습니다. 터미네이터가 엄지 손가락을 치켜세우며 뜨거운 쇳물 속으로 사라질 때, 왜 쇳물을 담고 있는 용광로는 녹아내리지 않는지에 대해서 말이죠.
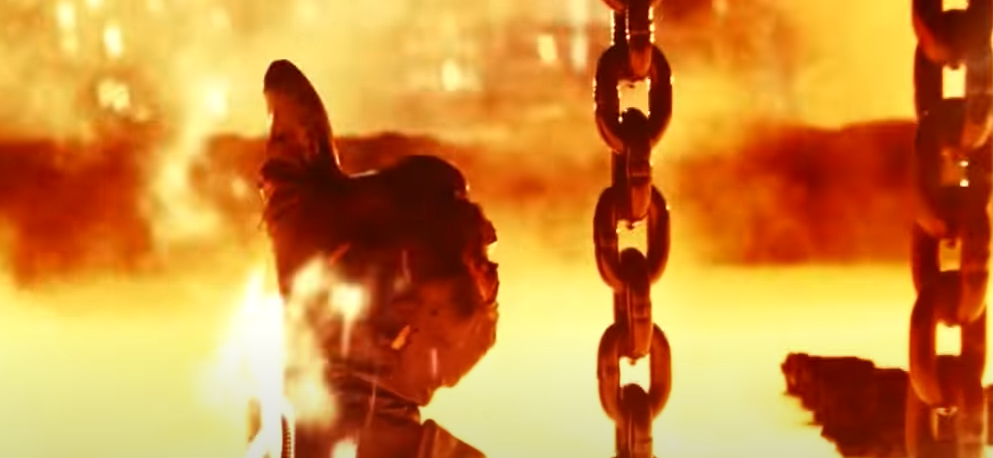
포인트는 ‘녹는점’에 있었습니다. 애석하게도 터미네이터의 로봇 팔은 용광로 속 쇳물보다 녹는점이 낮았던 것입니다. 이 때문에 훨씬 더 뜨거운 쇳물이 로봇 팔을 삼켜버린 것이죠. 그렇다면 이 쇳물을 담고 있는 용광로의 녹는점은 어떨까요? 영화 속 용광로가 어떤 재료로 만들어졌는지는 모르겠지만, 한 가지 확실한 사실은 쇳물보다 녹는점이 훨씬 높은 재료를 사용했다는 것입니다. 용광로의 녹는점이 어떤 쇳물보다도 높기 때문에 우리는 ‘쇳물 홍수’를 방지할 수 있게 되는 거죠.
자, 이제 녹는점의 원리를 제조의 세계에 적용해 봅시다. 뜨거운 쇳물을 이보다 녹는 점이 훨씬 높은 금형에 부어 원하는 모양으로 만든 뒤 식히면 제품을 만드는 가능하리라는 것을 이해할 수 있을 겁니다. 터미네이터, 쇳물, 용광로를 거쳐 오늘의 제조 길잡이 주제인 ‘다이캐스팅’에 대해 알아보겠습니다.
다이캐스팅(Die Casting)이란?
다이캐스팅은 영어 단어의 합성어입니다. 여기서 다이(die)는 ‘죽다’라는 뜻이 아니라 ‘금형’을 뜻합니다. 캐스팅(casting) 역시 ‘주물’이라는 뜻이죠. 말 그대로 다이캐스팅은 금형에 고열로 녹인 금속을 넣어 제품을 만드는 가공방식입니다. 보통 철로 된 금형 안에 알루미늄 등 여러 합금을 녹인 재료를 많이 사용하죠.
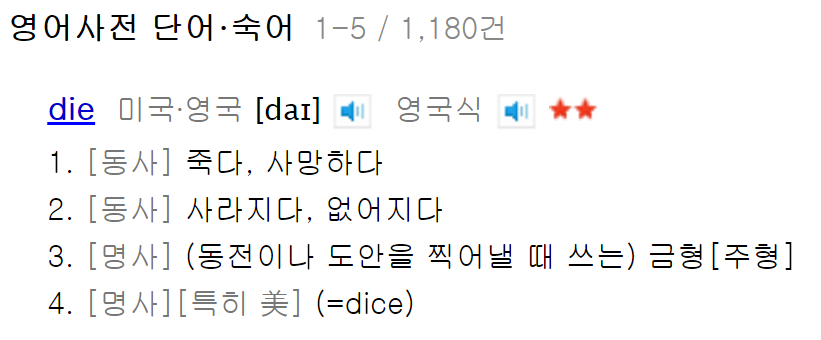
다이캐스팅은 주조의 한 갈래입니다. 주조의 세부 방식은 금형 자체가 소모적인지 영구적인지에 따라 큰 틀에서 두 가지로 구분합니다.
먼저 소모성 주형 방식들은 틀 안에 재료를 붓고, 주형을 부수고 깨서 제품을 꺼냅니다. 소모성 주형 방식에는 사형 주조, 셸 주조, 석고 주형 주조, 인베스트먼트 주조 등이 있죠. 영구적 주형 방식은 소모성 주형 방식과 달리 주형을 반복적, 영구적으로 사용 가능합니다. 주형을 부수지 않아도 제품을 꺼낼 수 있는 것이죠. 영구적 주형의 대표적 방식이 다이캐스팅입니다. 다이캐스팅 외에도 원심주조 역시 영구적 주형의 방식입니다.
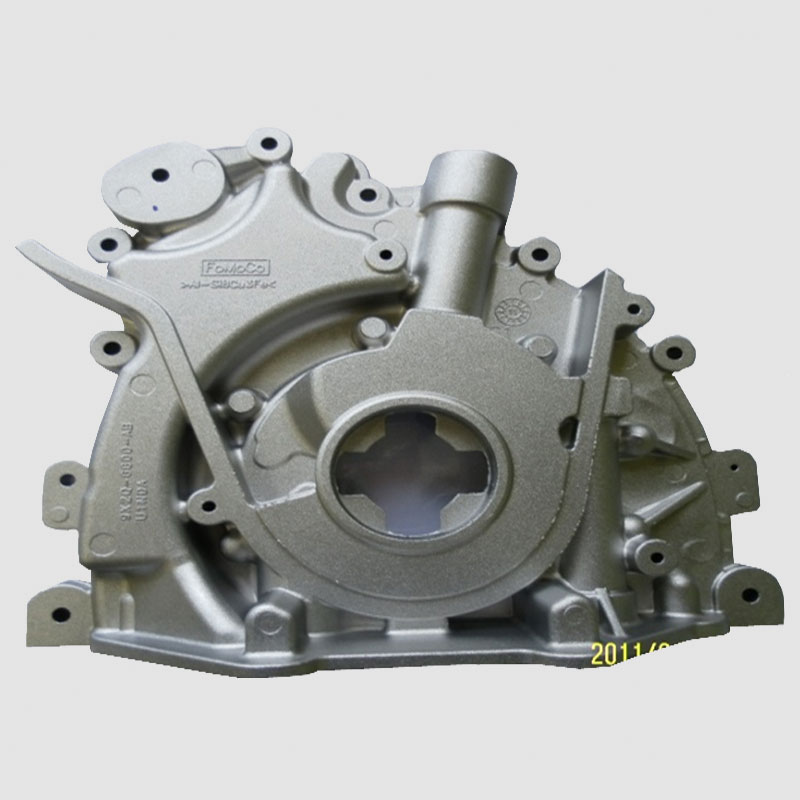
다이캐스팅은 일반적으로 복잡한 형상을 가진 제품이나 치수 정밀도가 높게 요구되는 부품을 생산하는 데에 적합합니다. 이미 만들어진 주형 틀에 재료를 부어서 찍어내기만 하기 때문에, 주형 틀을 정교하게 만들면 그만큼 정밀한 제품을 만들기 쉽겠죠.
일반적인 주조에서 쇳물을 주형에 흘려넣는 것과 달리 다이캐스팅에서는 보통 압력을 이용합니다. 즉, 금형 한 쪽에 연결된 주입구를 통해 쇳물을 주입할 때 높은 압력을 가해서 금형 틀 안으로 쇳물을 밀어넣습니다. 이처럼 압력을 사용해 강제로 밀어넣으면, 제품의 밀도와 강도를 균일하게 만들 수 있습니다. 쇳물을 주형 안으로 밀어넣었다면 압력을 유지한 상태로 금형 틀 안에서 냉각시킵니다. 압력을 유지한 채로 쇳물을 냉각시키는 이유는 금형 틀 안에서 쇳물이 빠져나오지 않고 균질한 상태가 유지되도록 하기 위함입니다.
사출성형과 유사··· 주재료는 알루미늄·아연·마그네슘
CNC가공, 금형사출, 판금 가공 등 각각의 제조 방식은 저마다 접근 방식이 상이합니다. 하지만 다이캐스팅과 금형사출만큼은 몹시 닮아 있습니다.
금형사출은 플라스틱 재료를 녹인 뒤 금형에 부어서 칫솔, 핸드폰 케이스 등 플라스틱 제품을 만듭니다. 다이캐스팅 역시 금형에 재료를 부어서 제품을 만들죠. 정밀하게 제작한 형틀에 재료를 부어서 찍어낸다는 점에서 정말 비슷합니다. 금형 사출과 다이캐스팅의 결정적인 차이점은 재료에 있습니다.
금형 사출에서는 주로 플라스틱을 녹여서 제품을 만들지만 다이캐스팅에서는 플라스틱보다 다루기 까다로운 금속 재료, 알루미늄, 아연, 주석 등의 비철금속을 재료로 사용합니다.
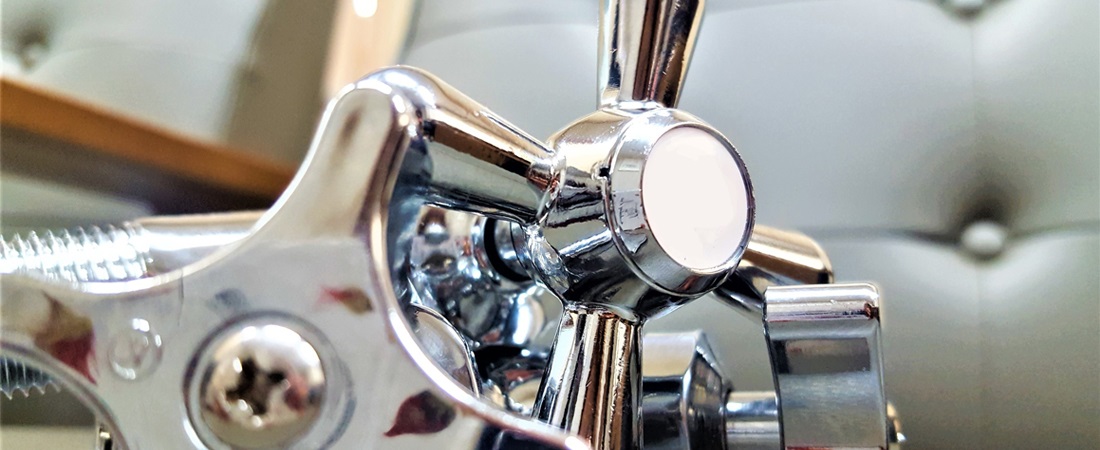
이러한 재료상의 차이 때문에 플라스틱보다 더 튼튼하게 힘을 견뎌야 하는 제품이나 부품을 다이캐스팅으로 만드는 경우가 많습니다. 자동차 부품이나 오토바이 부품, 공구, 기계 구조물처럼 쉽게 부러지는 것이 아니라 기계의 한 부품으로 단단하게 고정돼 기능해야하는 제품들입니다. 물론 이 외에도 사무기기나 가정용 기기 부품, 장난감까지 다양하게 생산할 수 있습니다.
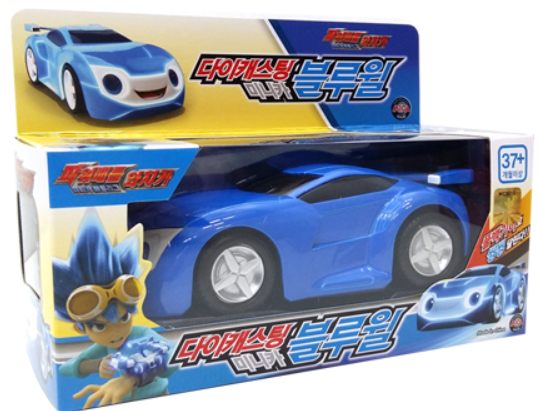
제품의 재료와 금형의 재료, 둘 중 어떤 재료의 녹는점이 더 높아야할까요? 터미네이터와 용광로를 다시 떠올려보세요. 금형의 녹는점이 제품의 녹는점보다 낮다면, 제품 재료보다 금형이 먼저 녹아내릴 것입니다. 이러한 불상사를 막기 위해서는 제품의 녹는점이 금형의 녹는점보다 반드시 낮아야 합니다.
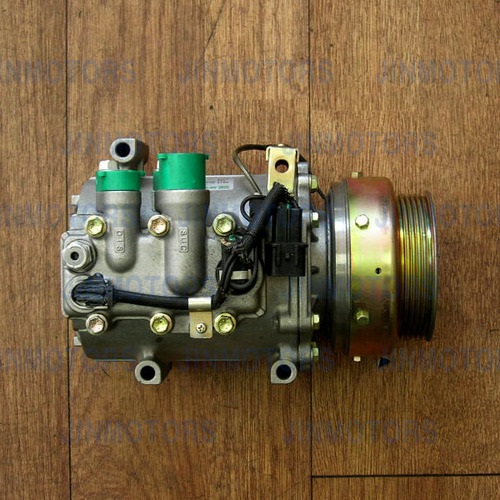
철은 녹는점이 높은 대표적인 금속입니다. 다이캐스팅으로 철을 가공하기보다는 다이캐스팅에 사용할 금형 틀을 철로 만드는 경우가 많은 것은 이 때문입니다. 대신 상대적으로 녹는점이 낮은 소재, 비철금속은 다이캐스팅 제품의 재료로 사용됩니다. 알루미늄과 아연, 마그네슘 등 세 가지가 다이캐스팅의 주 재료로 사용되는 대표적인 합금입니다.
알루미늄은 가볍습니다. 그러면서도 강도와 경도가 우수해 제품의 무게를 줄이는 데 유리합니다. 아연은 강도가 높고 경도가 뛰어납니다. 기계 가공이나 프레스, 스탬프 및 조립 부품으로 적절한 재료입니다. 마그네슘은 강하고 단단합니다. 완전히 재활용도 가능한 데다 가볍습니다. 무게를 줄이는 것이 중요한 제품을 만들 때 적합합니다.
다이캐스팅에 사용되는 합금들은 내식성(금속 부식에 대한 저항력)이 우수합니다. 대체로 강도와 경도도 높습니다. 열전도율도 높고 전기전도성도 우수해 다양하게 활용할 수 있습니다.
쇳물 가열 여부에 따라 구분
다이캐스팅 공정에서는 쇳물이 일정한 압력(0.7~700MPa)으로 금형에 주입되면서 제품이 만들어집니다. 이때 쇳물을 가열해서 주입하는지, 주입 후에 가열하는지에 따라 크게 고온챔버 다이캐스팅과 저온챔버 다이캐스팅으로 구분합니다.
고온 챔버 다이캐스팅
금형에 주입하기 전에 쇳물을 미리 가열합니다. 가열된 쇳물을 피스톤의 압력을 이용해 금형 안으로 밀어넣습니다. 쇳물이 금형 안에서 굳을 때까지 압력(평균 15MPa, 최대압력 35MPa)은 계속 가합니다. 쇳물이 금형 바깥으로 빠져나오지 않게 하기 위해서입니다.
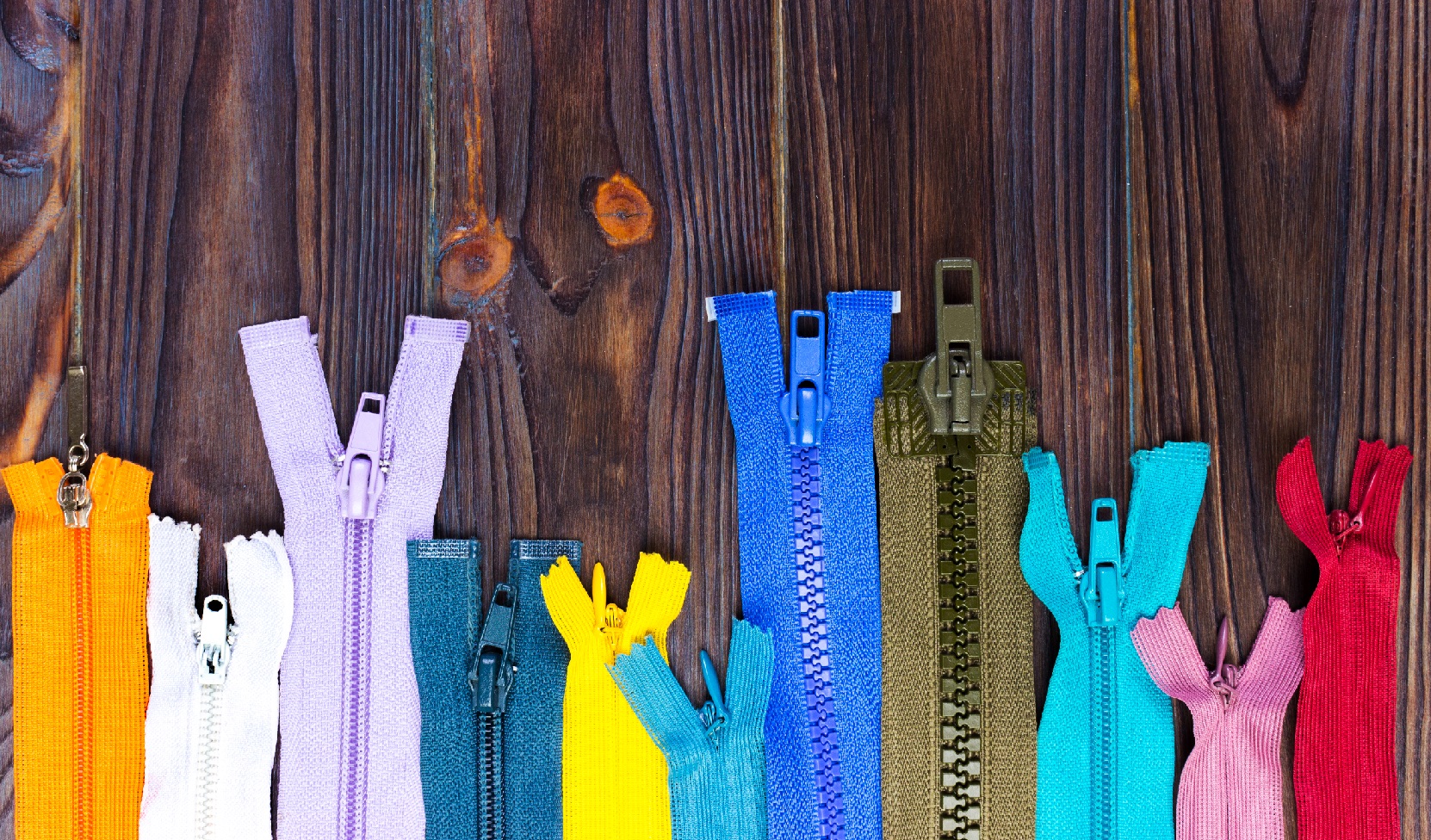
금형의 녹는점은 재료의 녹는점보다 높지만, 계속해서 열이 가해지면 시간이 지날수록 손상됩니다. 금형의 손상을 방지하면서도 신속하게 제품을 만들어내기 위해 금형을 물이나 기름으로 냉각합니다. 위 과정을 거쳐 제품을 만들어내는 주기를 사이클이라고 합니다. 사이클 시간은 아연의 경우 시간당 200~300회정도 입니다. 지퍼 이(zipper teeth)와 같이 작은 부품의 경우는 시간당 최대 1만8천회 정도의 사이클을 가집니다.
고온챔버 다이캐스팅 공정은 쇳물을 미리 담아놓고 자체적으로 가열합니다. 때문에 공기의 유입이 적어 산화물의 생성이 적습니다. 저온챔버 방식보다 상대적으로 주조 사이클이 빨라 생산성이 높습니다. 쇳물 온도를 제어하기도 용이합니다. 하지만 소모품의 가격이 고가입니다. 부품 교체에 시간이 어느 정도 소모되는 편입니다.
저온 챔버 다이캐스팅
쇳물을 가열하지 않은 채로 외부에서 주입한다는 점이 차이점입니다. 저온챔버 방식에서 쇳물은 분사 실린더(주입 챔버)로 주입되는데 이때 챔버는 가열되지 않습니다. 쇳물을 밀어넣는 압력은 저온 챔버 방식(20~770MPa, 최대압력 150MPa)이 고온 챔버 방식보다 더 높습니다.
저온챔버 방식으로는 황동이나 청동처럼 상대적으로 녹는 점이 더 높은 금속을 주조하는 데 적합합니다. 알루미늄, 마그네슘, 구리 등도 저온챔버 방식에 적합한 재료입니다. 또 저온 챔버 방식을 통해 고온챔버 제품보다 더 단단한 제품을 만들 수 있습니다.
저온 챔버 방식은 대형 제품 생산에 용이합니다. 저온 챔버 공정의 소모품도 가격이 저렴한 편이고 교체가 간편합니다. 사출력과 생산성이 모두 높으므로 다양한 두께의 제품을 만들 수 있습니다. 하지만 주조 사이클이 상대적으로 늦습니다. 매 사이클마다 보온로에서부터 용해된 금속을 채워넣어야 하기 때문에 주조 사이클이 고온챔버 방식보다 길어지기 때문입니다. 쇳물 온도를 제어하기도 쉽지 않고, 공기의 유입이 커서 산화물이 많이 생성된다는 것은 단점입니다.
지금까지 다이캐스팅 주조 장비의 종류에 따라 저온 챔버 공정, 고온 챔버 공정으로 구분해봤습니다. 다이캐스팅은 일반적으로 고속, 고압 주조법으로 알려져있지만, 쇳물의 압력과 충전속도에 따라서도 세부적으로 분류할 수 있습니다. 가압력 10kg/㎠이하를 저압, 10~500km/㎠를 중압, 500kg/㎠ 이상을 고압으로 분류합니다. 충전 속도는 0.05~1.5m/sec를 저속, 10~60 m/sec을 고속으로 분류할 수 있습니다.
長: 금형 반복 사용해 신속한 작업에 유리
앞서 설명한 대로 다이캐스팅은 영구적 주조로 분류됩니다. 즉, 금형을 반복적으로 사용할 수 있습니다. 신속한 작업에도 적합합니다. 고온 챔버 방식의 경우 보통 시간당 500회 정도까지 사이클이 돌아갑니다. 대량생산을 하게 되면 단가를 줄일 수 있고 폐기되는 재료도 적어 비용이 절약됩니다.
또한 두께 0.5mm이하의 정밀한 제품, 복잡한 형상의 제품도 생산이 가능합니다. 주물의 표면이 깔끔하고 곱기 때문에 표면에 도장, 도금할 때 다듬질 작업을 줄일 수 있습니다. 제품 조직이 치밀해 강도가 높습니다. 여러 개의 부품을 하나의 부품으로 합칠 수도 있습니다. 조립 작업을 없앨 수 있는 셈입니다. 부품 일관성도 높아집니다.
短: 금형제작 비용 높아 소량 생산엔 부적합
금형 제작에 비용이 많이 든다는 것이 가장 큰 단점으로 꼽힙니다. 이처럼 초기 비용이 매우 높기 때문에 소량 생산에는 부적합합니다. 고온/저온 챔버 방식에 상관없이, 일정 시간 동안 가둬놓고 고온 상태를 유지할 수 있는 재료를 선택해야 하기 때문에 가공할 수 있는 재료 선택에 제한이 있습니다. 또 제품 생산후 구멍을 별도로 뚫어야 하는 등 후처리나 후가공이 필요한 경우가 많기 때문에 이 또한 단가를 높이는 요인이 됩니다.
온라인 제조 플랫폼 캐파(CAPA)에서는 다이캐스팅을 비롯한 다양한 방식의 가공 기술을 보유한 전문가 파트너(제조업체)를 만날 수 있습니다. 캐파에는 2300여 파트너(공정 합산 기준)가 고객들의 주문을 기다리고 있습니다.