설계부터 제작까지 한번에
“무엇이든 만들어 드립니다”
“저희 수모델링은.. (탕탕탕!) 설계부터 제작까지.. (쓱싹쓱싹~)”
인터뷰 중간중간 두드리고 깎는 소리가 인터뷰이의 대답 사이사이를 비집고 들어온다. 사무실 한 쪽에서 후처리 작업이 한창인 바쁜 움직임들이 만드는 소리다. 낡은 작업용 앞치마를 두른 직원들의 이마에는 굵은 갈매기 주름이 깊게 패여 있다. 주름의 깊이는 노련함의 증표다.
수모델링은 기구설계부터 가공까지, 시제품 제작의 모든 과정을 담당하는 시제품 제작 전문 업체다. 시제품 분야에도 분업이 주를 이루다 보니 설계부터 제작까지 도맡는 업체는 흔치 않다. 시제품 제작이란 한 분야에서 15년을 갈고 닦아온 한상철 수모델링 대표를 경기도 광명의 사무실에서 만났다. 아래는 한상철 대표와의 인터뷰 전문.
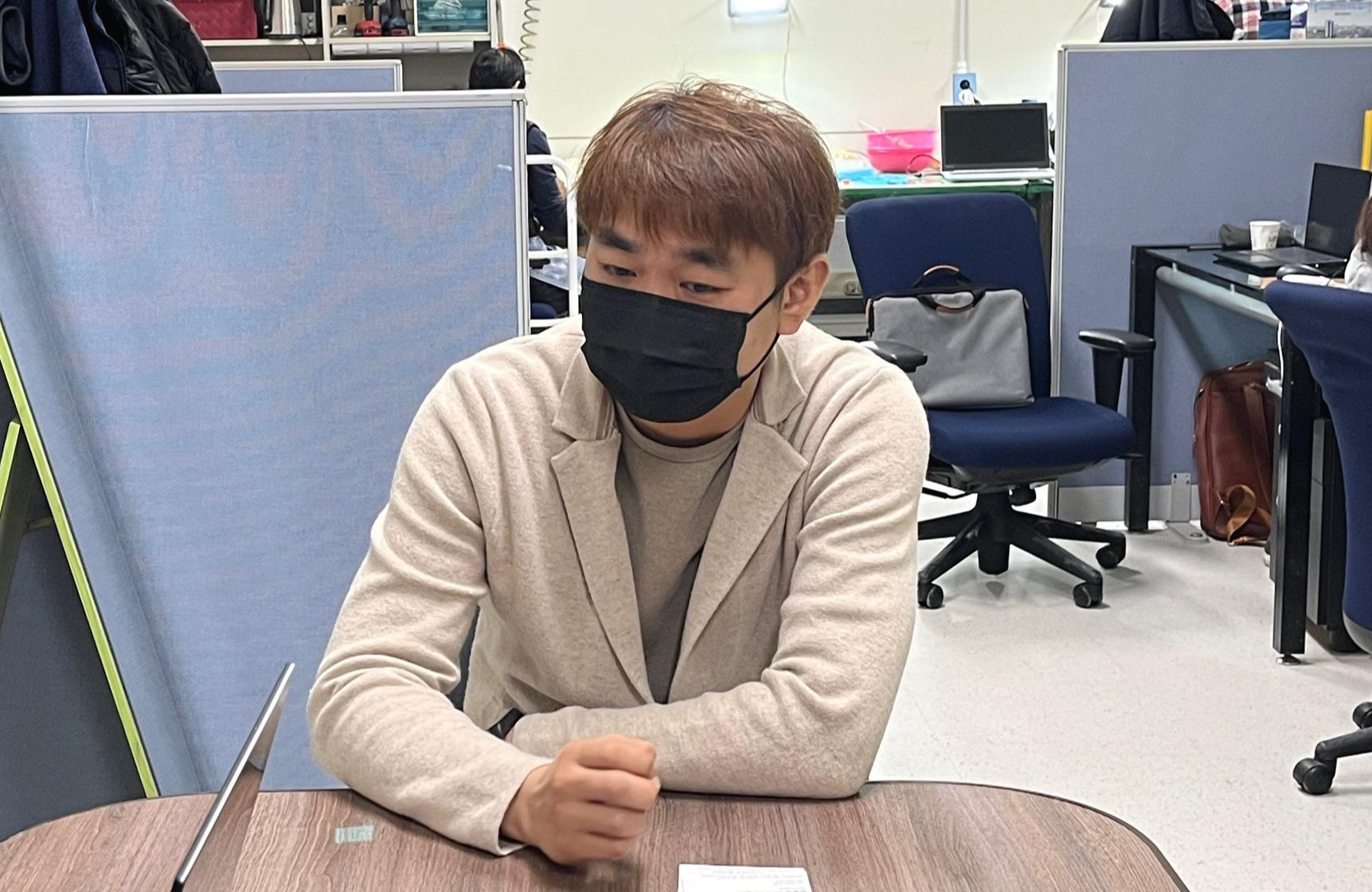
Q> 인터뷰 전부터 사무실 안에서 바쁘게 작업하는 직원들이 눈에 띈다
“수모델링은 설계만 하지는 않는다. 기구설계부터 제품 제작까지 전 단계를 다룬다. (사무실) 뒤 쪽 현장은 제품 표면을 다듬는 후처리 작업이 이뤄지고 있는데, 모두 경력만 수십 년되는 전문가 분들이다. 도색 작업도 가능한데, 사무실 안 쪽 방 전체가 도색 공간이다.”
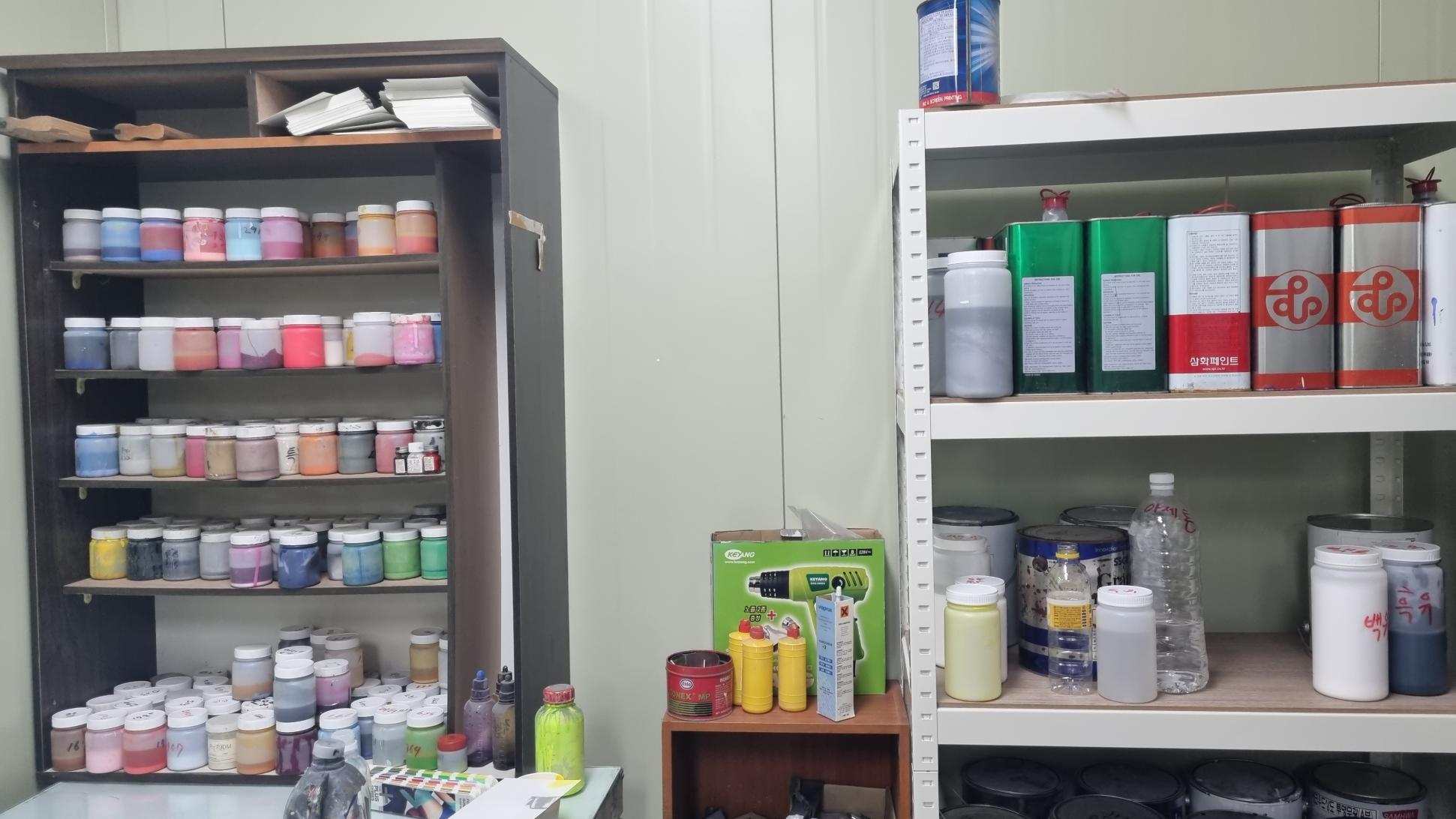
한상철 대표가 가공 현장도 보여주겠다며 또 다른 사무실로 안내했다. 별도로 마련된 제2 사무실에는 CNC 가공 기계 4대가 모두 바쁘게 돌아가고 있었다. 작업용 앞치마를 두른 직원 2명이 캐파(CAPA)팀을 맞았다. 모두 옷에 하얀 가루들이 잔뜩 묻어있었다. 먼저 인사를 건네기 전까지 인기척을 못 느낀 채 작업에 몰두하고 있는 직원도 있었다.
Q>회사 안이 ‘미니(mini) 공장’같다. 이곳에서 설계부터 시제품 제작까지 한 번에 진행할 수 있나
“그렇다. 설계부터 가공까지 (각각) 어떤 업체에 맡겨야 할지 몰라 고민하는 초보 고객들이라면, (모든 공정을 한 곳에서 끝내기 때문에) 보다 쉽게 제조에 접근할 수 있는 셈이다. 단순히 설계부터 제작까지 한 번에 끝낼 수 있다는 장점만 있는 건 아니다. 제품을 완성도 있게 만드는 건 기본이고, 거기에 더해 쉽게 제작할 수 있다는 의미다. 정밀하고 완성도 높은 제품을 만드는 것을 가장 중요한 목표로 작업을 하고 있고 그 부분에서는 자신 있다.”
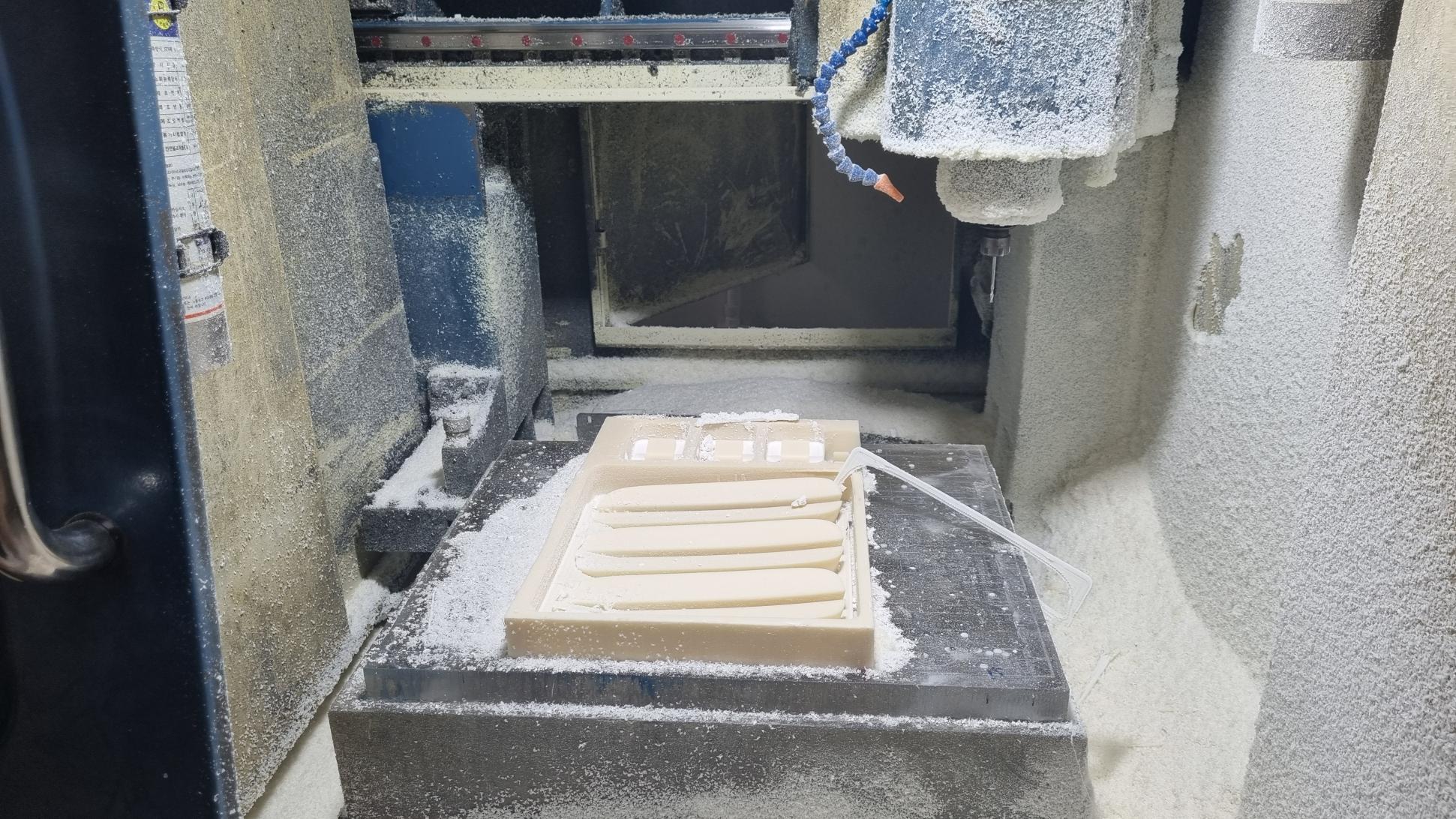
Q>시제품 제작에서 가장 중요시하는 부분이 있다면?
“시제품은 본제품이 어떻게 작동될지를 제대로 보여줄 수 있어야 한다. (최종 제품이) 판매용이라면 시제품은 종종 투자자들에게 선보일 샘플이 되기도 한다. 시제품이 중요한 이유다.
그런데 만약 시제품이 조립이 안 된다면 치명적인 문제가 된다. 2018년 평창 패럴림픽 때 사용된 VR글래스를 수모델링에서 제작했다. 이 제품도 정밀도에서 공을 들였던 제품이다. 일단 사람이 착용하는 제품이고, 착용한 사람이 움직여야 하기 때문에 안전성과 정밀도가 모두 중요했다. 만들어놓고 보니 형합(조립)이 잘 안 됐다. 누적공차가 발생한 탓이었다. 제품에 공차를 더 주거나, 부품 위치를 바꾸거나, 나사를 더 꽉 조이는 등 이리 저리 고민한 끝에, 3번만에 최종 제품을 만들 수 있었다.”
참고로 AR글래스는 평창 패럴림픽 성화봉송의 숨은 기여자다. 평창 패럴림픽 때 전신 마비 장애인이 웨어러블 슈트를 착용하고 성화 봉송 주자로 나섰다. 이 웨어러블 슈트의 상태를 확인하는 데에 AR글래스가 활용됐다.
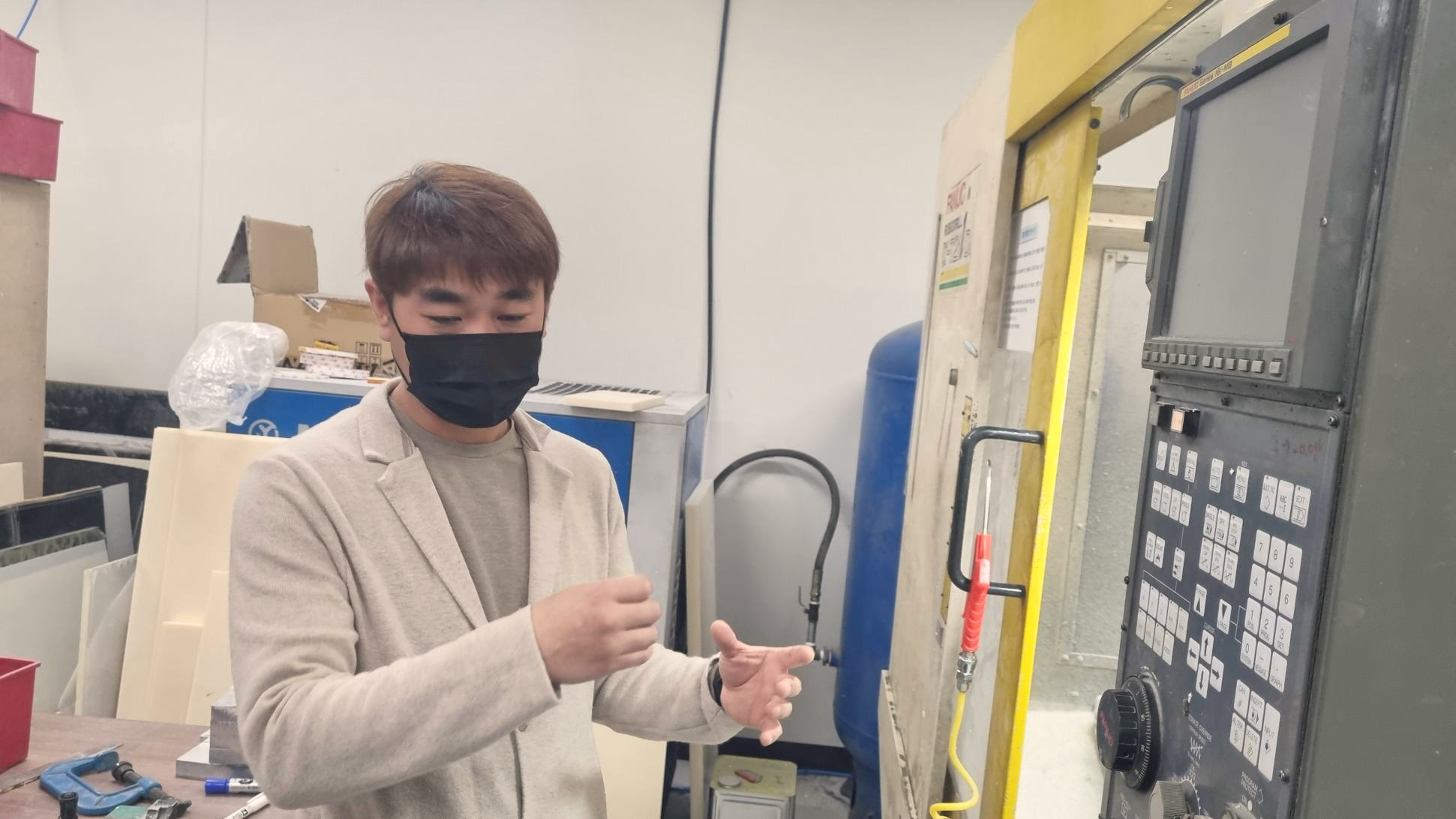
Q>평창 패럴림픽 AR글래스 제작엔 어떻게 참여하게 됐나
“설계는 LG전자에서 담당하고, 제작은 수모델링이 했다. LG전자와 협업을 하고 있어서 가능했다. AR글래스뿐만 아니라 스마트워치도 만들었다. AR글래스는 평창 패럴림픽 때 100여 개 정도 만들었다. 제작하는 데 2개월 가량 걸렸다. 많은 사람들 앞에서 수모델링 제품을 소개할 수 있었던 기회여서 의미가 남달랐다.”
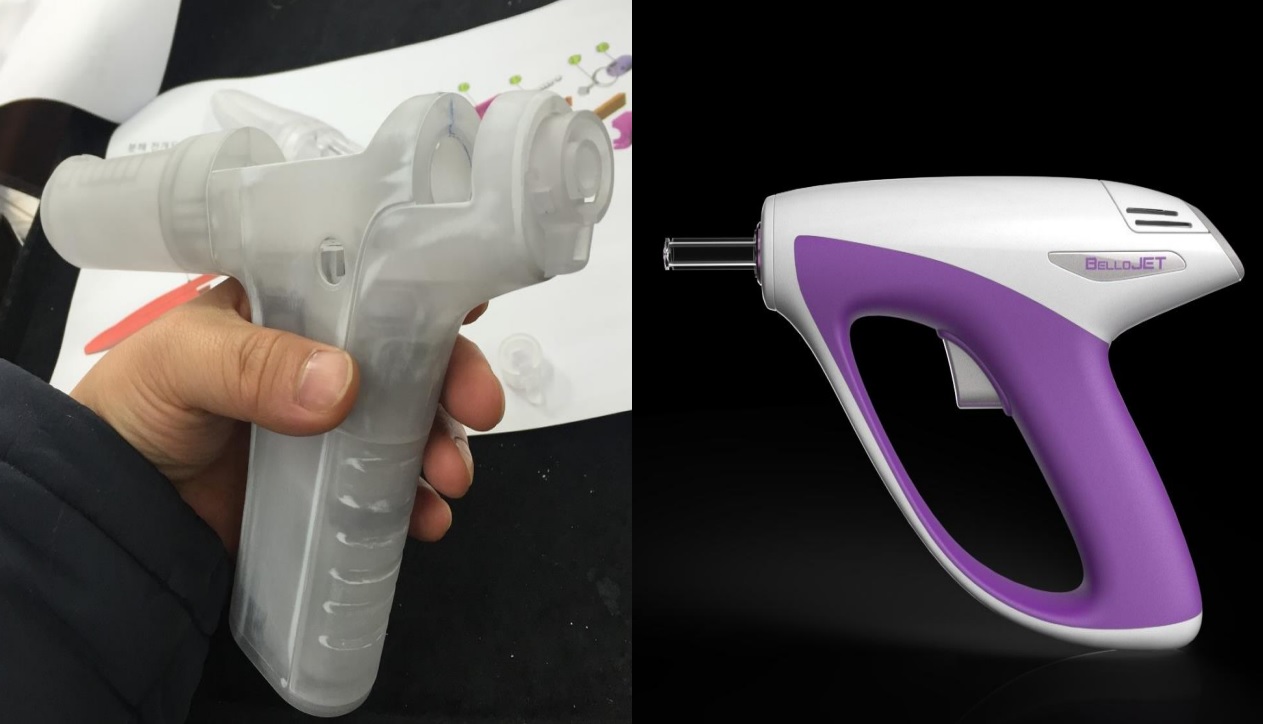
Q>시제품은 본제품을 잘 만들기 위한 기초라는 말을 하곤 한다
“어떤 제품도 한 번에 만들어지는 제품은 없다. 기구설계부터 원하는 제품을 완성하기까지 짧게는 3개월, 길게는 1년까지, 때로는 그 이상도 걸린다. 시간이 많이 걸리는 이유는 제작 과정에서 마주하는 수많은 변수와 문제들을 해결해야하기 때문이다. 완성도 높은 제품은 수많은 시행착오들을 반복하고, 수정하는 작업을 거친 후에야 나올 수 있다.”
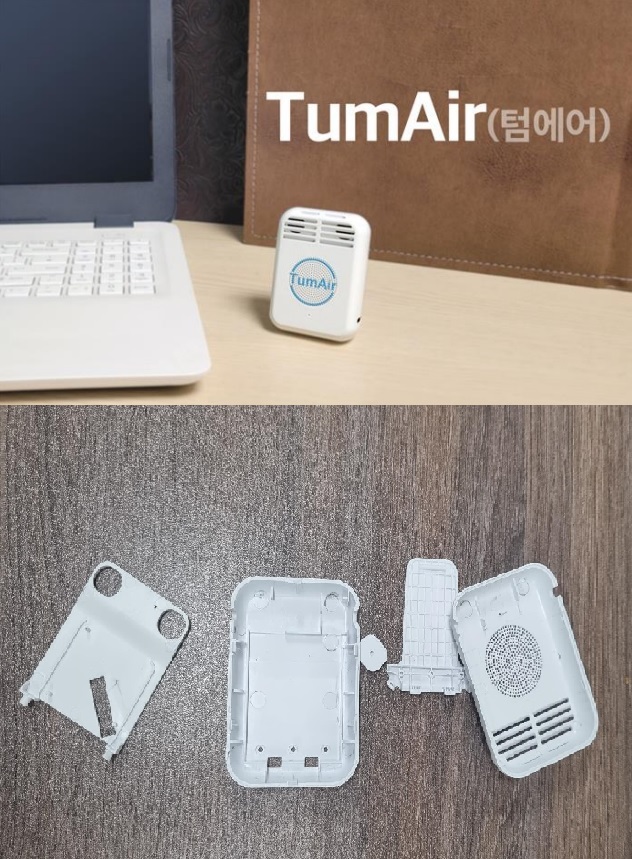
Q> 시제품 제작 과정에서 예산 등의 문제로 난관에 부딪히는 일도 적지 않을 것 같다
“한 번은 제품에 들어가는 필수 하드웨어 부품을 못 구해서 고생했던 적이 있다. 부품을 고를 때 어느 정도 가격대를 선택할 것인지, 어떤 브랜드 부품을 고를지까지는 고객이 아닌 수모델링의 몫이다. 적당히 유사한 기능을 할 수 있는 부품으로 대체할 수는 없다. 고객이 요청한 대로 기능해야하는 것은 기본이고, 고객이 요청한 단가도 맞춰야 하기 때문에 적절한 가격의 제대로된 부품을 찾아내야 한다.
Q> 구체적으로 설명해 줄 수 있나?
“면도기에서 젤이 나올 수 있도록 고안한 제품이었다. 기구설계에는 한 달밖에 안 걸렸다. 문제는 젤을 나오게 하는 펌프 부품을 국내에서 마땅히 찾을 수 없었다. 고객이 요청한 단가를 고려하면 (국내 부품은) 터무니없이 가격이 비쌌다. 과거에 활용했던 펌프 기술로 대체해 봤지만, 젤의 점성이 강해서 (젤이 밖으로) 잘 나오지 않았다.
지인부터 시작해서 여기저기 전화도 해보고, 구글링으로 세계 각지에 부품들을 수소문하기 시작했다. 결국 3개월 만에 중국의 한 회사에서 부품을 구할 수 있었다. 제품에 실제 사용한 중국산 부품 가격은 처음 국내에서 찾았던 부품 가격의 10분의 1 수준이었다.”
Q> 만약 값싼 부품을 구하지 못했다면 어떻게 됐을까
“펌프 부품 하나 때문에 제작을 포기해야 할 수도 있었다. 다행히 우리 쪽에서 적절한 부품을 찾아내 적정 단가에 맞는 제품을 만들 수 있었고, 고객도 굉장히 흡족해했다. 저 역시 뿌듯했다. 단가가 정해지면 양산까지 고려해 흐름을 잡을 수 있다. 제품 하나에 나사 2개가 추가돼 100원이 더 든다고 하면 별 것 아닌 것 같지만, 제품 10만개를 만든다고 치면 1000만원, 100만개를 만든다면 1억원에 이르는 비용 차이가 날 수 있다.”
끝으로 한상철 대표에게 캐파(CAPA)를 통해 만날 예비 고객들에게 전하고 싶은 말이 있냐고 묻자 “무엇이든 만들어드릴 수 있다고 전하고 싶다”며 웃었다.
자사의 기술력을 뛰어넘는 제품까지 무턱대고 다 만들 수 있다는 식의 근거 없는 자신감의 표현은 아니었다. 고객의 요청이 있다면 1개월이든 3개월이든, 필요한 부품이 있다면 전세계를 뒤져서라도 기필코 만들어내겠다는 근성을 드러내는 것으로 느껴졌다. 자신만의 아이디어를 제대로 된 제품으로 만들고 싶다면, 한상철 수모델링 대표의 ‘집요함’을 믿어봐도 좋을 듯하다.
* 캐파(CAPA) 회원에 가입하면 시제품 제작에 전문성을 가진 ‘수모델링’을 비롯한 국내 최고의 경쟁력을 갖춘 2200여 제조업 파트너(공정 기준)를 만나실 수 있습니다.