얼핏 보기에 압출과 사출 성형은 매우 유사한 제조 공정 같습니다. 실제로 두 공정 모두 기계를 통해 용융(鎔融)된 재료를 이용해 원하는 형태의 제품(부품)을 비교적 싼 비용으로 대량 생산해 냅니다. 두 공정 모두 부품 생산량이 많아질수록 비용이 낮아지는, 양산에 적합한 제조 방식이죠. 하지만 사출 성형과 압출은 이름에서도 나타나듯 세부적으로 들여다 보면 적지 않은 차이점이 존재합니다.
오늘은 얼핏 보면 비슷한 사출 성형(Injection Molding)과 압출(Extrusion)에 대해 다뤄보겠습니다. 두 공정의 유사점과 차이점을 비롯해 제조 공정 상의 장단점, 비용 및 응용 분야를 살펴봄으로써 각각의 공정이 어떤 제품을 생산할 때 적합한 지 알아보겠습니다.
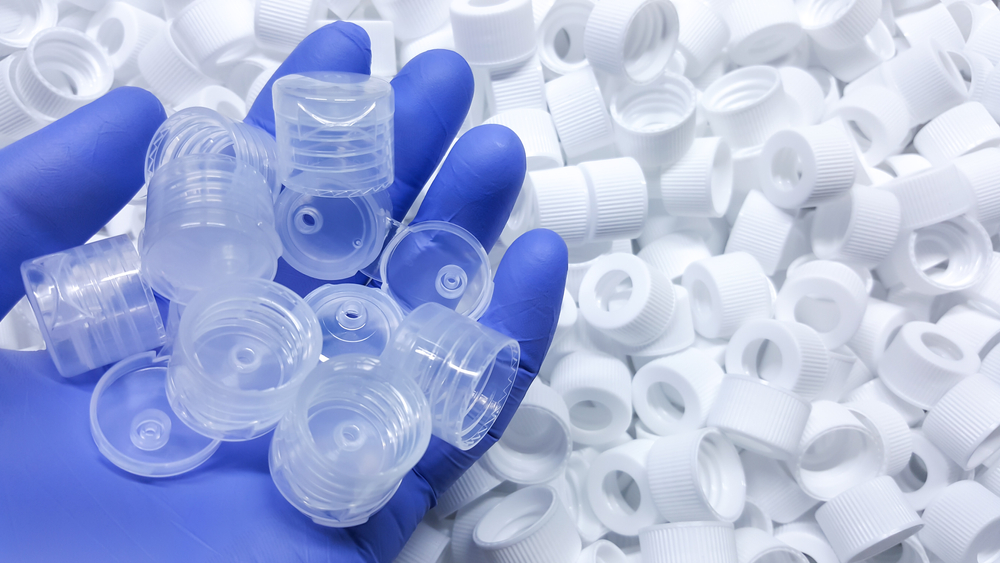
사출성형: 플라스틱 재료를 저렴하게 대량 생산
사출 성형은 플라스틱 제품을 경제적인 비용으로 대량 생산할 수 있는 가장 대표적인 제조 방법입니다.
사출 성형 공정을 구체적으로 살펴보면 먼저 플라스틱 재료(수지)를 고열로 녹인 다음 ‘금형’에 주입합니다. 냉각된 제품을 금형에서 꺼낸 뒤, 표면 마감 등 후공정을 거쳐 복잡한 3차원 형상을 만듭니다.
이상의 동일한 공정을 수백 또는 수천 번 빠르게 반복함으로써 금형 제작 비용을 상각하고 제품 생산 비용을 절감할 수 있습니다. 각 부품에 동일한 금형 도구가 반복 사용될 뿐만 아니라 플라스틱 성형 재료인 ‘펠릿’이 매우 저렴하기 때문에 사출 성형은 일관된 품질의 저렴한 부품을 생산하는 데 적합합니다.
장점
- 동일한 재료를 사용한 3D 프린팅과 같은 여타 공정과 비교해 품질이 우수한 편입니다.
- 사출 성형에 사용되는 금형은 CNC 가공을 통해 높은 수준의 정밀도와 공차를 보장하며 작고 복잡한 부품을 동일한 퀄리티로 양산할 수 있습니다.
- 3D 프린팅 및 CNC 가공에 비해 재료나 색상, 광택 및 질감 등의 측면에서 다양한 선택지를 제공합니다.
- 전용 금형만 있다면, 생산 주기가 30초 이하인 부품 수천 개를 매우 빠르게 생산할 수 있습니다.
- 사출 성형은 매우 빠르게 발전하는 기술이기 때문에 시간이 지남에 따라 장점이 더욱 커질 전망입니다.
단점
- 금속 부품을 대량 생산할 수 있는 금속 사출 성형 기술이 존재하지만, 아직까지 대체로 플라스틱 부품을 만드는 경우에 국한돼 사용됩니다.
- 본격적인 제품 생산에 앞서 금형을 제작하는 데에 상당한 시간이 소요됩니다. 이는 제품 생산의 리드 타임(더 알아보기)을 증가시키기 때문에 프로토타입(시제품) 생산이나 소량 제작에 있어서는 3D 프린팅이나 QDM(더 알아보기)에 비해 불리합니다.
- 환경에 대한 경각심이 높아지면서 플라스틱 제품을 대량 생산하는 사출성형에 대해서도 비판적인 목소리가 나오고 있습니다. 전력 사용량도 상당히 많습니다.
- 주문량이 금형 제작 비용을 상쇄하고 남을 만큼 충분하지 않다면 비용 부담이 큽니다. 초창기 스타트업이나 중소량의 제품을 생산하는 업체에 다소 부담되는 선택지일 수 있습니다.
압출 공정: 플라스틱은 물론 금속도 커버
압출 공정은 고온의 재료를 금형에 주입해 형태를 만든다는 점에서 사출 성형 방식과 비슷하지만, 형태가 일정하고 길이가 긴 제품을 만드는 데 효율적입니다.
압출기를 통과한 재료는 압출기 끝 부분에 장착된 다이(Die)를 통과하면서 복잡한 교차-단면, 외부 모양 및 내부 빈 공간이 있는 막대 모형의 성형물을 만듭니다(하단의 사진 참고). 금형의 모양이 사출성형 제품의 형태를 결정하듯이, 압출 공정에서는 다이의 모양에 따라 제품의 형태가 결정됩니다.
종종 30미터에서 300미터 길이에 이르는 복잡한 모양의 긴 막대는 일반적으로 띠톱으로 자르거나 모양을 변형하는 등 후공정을 통해 형태를 수정하거나 다른 생산 공정에 배치할 수 있습니다.
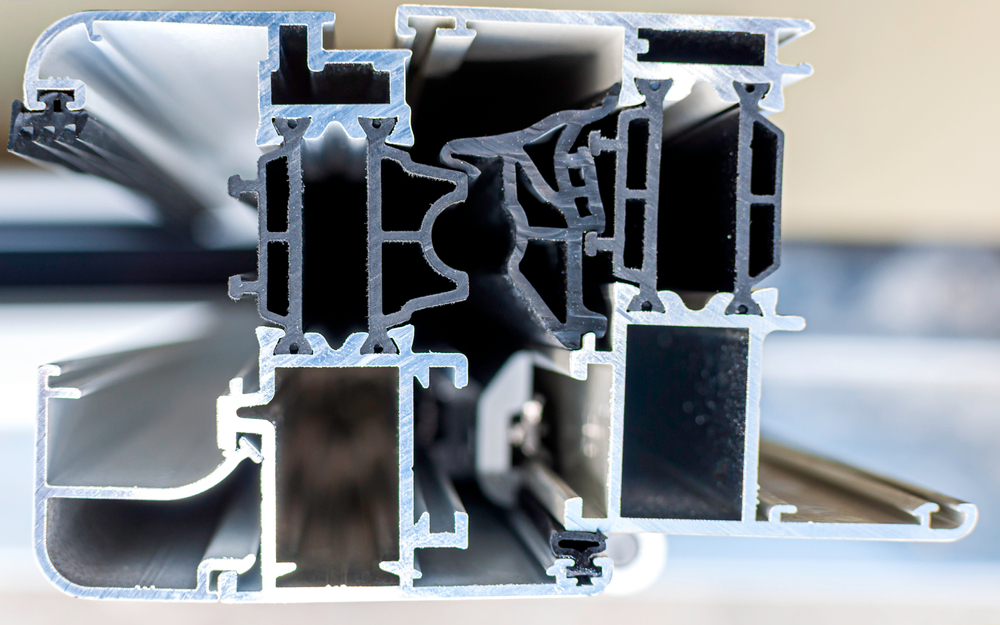
장점
- 압출 공정의 재료로는 플라스틱은 물론, 금속도 두루 사용됩니다. 금속 재료의 경우 알루미늄이 가장 일반적(약 80% 차지)이며 플라스틱 재료로는 폴리프로필렌이 가장 일반적으로 사용됩니다.
- 열간 압출, 냉간 압출, 마찰 압출 등 다양한 유형의 압출 방식을 통해 고유한 특성의 제품을 생산해낼 수있습니다.
- 금속 압출의 경우 CNC 가공과 같은 다른 금속 공정보다 훨씬 저렴합니다.
단점
- 정교하게 제작된 금형을 통해 형태가 결정되는 플라스틱 사출 성형만큼 정교한 제품을 생산하기는 어렵습니다.
- 사출 성형과 마찬가지로 플라스틱과 금속 제품을 생산하는 과정이 환경 측면에서 높은 비용이 발생합니다.
- 다른 제조 방법, 특히 사출 성형과 비교할 때 재료의 선택지가 훨씬 적습니다.
사출 성형과 압출 공정의 장단점을 정리하면 아래와 같습니다. 각각의 장단점을 숙지한 뒤 자신에게 맞는 제조 공정을 선택하는 것이 유리합니다.
사출 성형 | 압출 | |
장점 | – 비교적 정밀도가 높고 품질이 좋은 편. – 재료나 색상, 광택 및 질감 등의 측면에서 다양한 선택지 제공. – 빠른 생산. – 잠재력이 높은 기술. | – 재료 접근성이 높음. – 다양한 압출 방법을 사용할 수 있음. – 비용이 훨씬 저렴함. |
단점 | – 주로 플라스틱을 원료로 생산. 금속 생산에는 한계. – 금형 제작 시간을 포함하면 제작 기간이 다소 긴 편. – 환경 비용이 높음. – 초기 비용이 높음. | – 정교함 부족. – 환경 비용이 높음. – 재료 범위가 제한됨. |
비싼 금형 비용 VS 높은 단가
사출 성형과 압출, 두 공정은 더 낮은 비용으로 부품을 대량 생산할 수 있다는 점에서 유사합니다. 단, 두 공정의 비용 동인이 다르다는 점을 유의해야 합니다.
사출 성형은 금형 초기 제작 비용이 높지만, 제품 양산 과정에서 초기 비용을 빠르게 회수할 수 있습니다.
이에 비해 압출 공정의 금형 비용은 사출 성형보다 80%에서 90% 저렴하여 초기에는 비용이 덜 들지만, 개당 생산 비용이 사출 성형보다 약간 더 높은 편입니다.
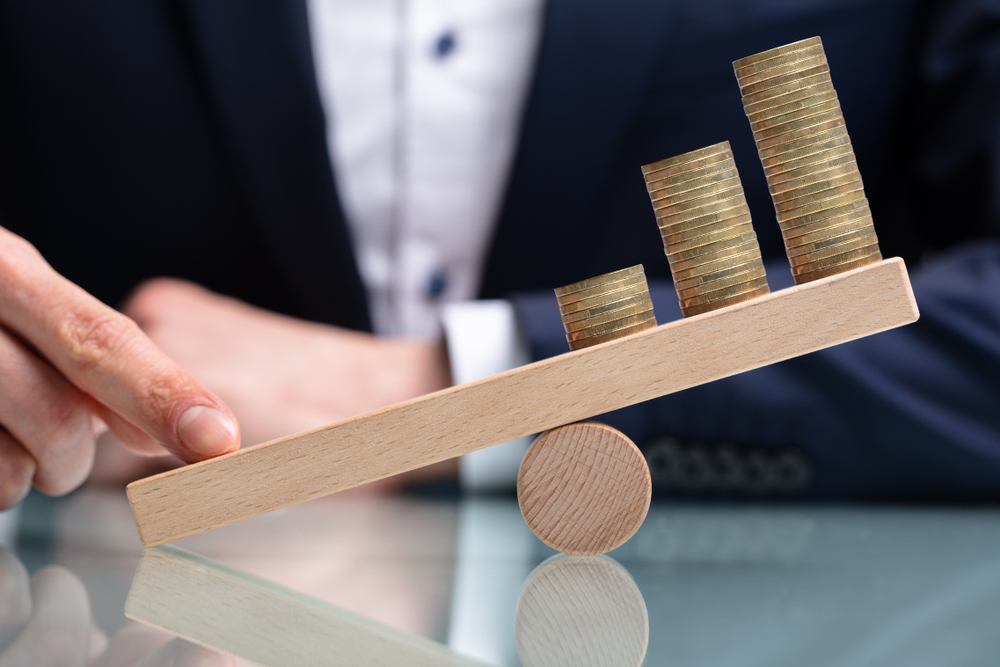
각각에 적합한 산업군은?
사출 성형과 압출은 각기 다른 특성에 맞게, 주로 사용되는 산업 영역도 조금씩 다릅니다.
플라스틱 사출 성형은 우리 일상생활에서 가장 쉽게 찾아볼 수 있는 가공 방식입니다. 항공우주, 의료 기기, 소비재, 에너지, 전자, 자동차, 로봇 및 장난감 산업 등 광범위한 영역에 적합합니다.
이에 비해 압출은 역시 항공우주 및 자동차 산업에서 사용되지만 특정 분야에 국한돼 사용됩니다. 이 외에도 사다리, 비계, 컨베이어, 공정 제어, 농업, 건축, 골조 및 광업에 두루 사용됩니다. 플라스틱 압출의 경우 ‘파이프, 판재, 필름 및 와이어 커버링’과 같은 제품을 만드는 데 유용합니다.
온라인 제조 플랫폼 캐파(CAPA)에서는 최고의 전문성을 갖춘 제조 파트너를 만날 수 있습니다. 사출 성형 혹은 압출 가공방식을 통해 제품을 생산하고 싶다면 지금 캐파에 접속해 캐파의 제조 전문 파트너와 상담해보세요.